All of our steering robots have an angular encoder built in; a feedback device that reports back to the control system what angle the steering robot is at.
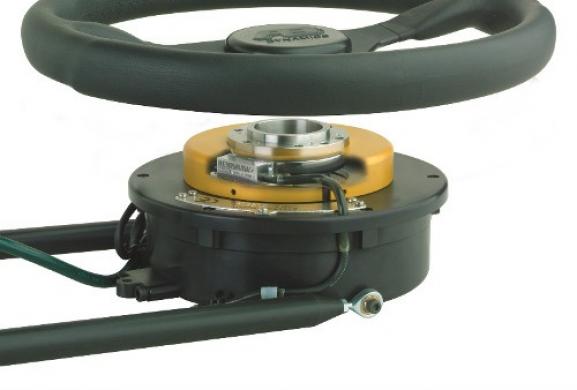
Every control loop needs a feedback signal – a measure of “where I am now” which it can compare with “where I should be now” to generate corrective action. When a steering robot is controlled in angle mode, the feedback device is the angular encoder. We use a range of encoders in our driving robots to suit the particular requirements of each actuator.
These include optical encoders, such as the Renishaw system in the SR30 steering robot shown above, magnetic devices and inductive encoders.
The definition of a steering input as required by a test standard will include an angular input (e.g. turn the steering 90 degrees to the left) and – normally – a tolerance, which might be +/-1 degree. The tolerance defines whether an input of 90.5 degrees is acceptable or not if the target is 90 degrees.
Historically, tolerances would have been defined based upon what an expert human driver could achieve. Today, a robot can achieve accuracies far beyond what any human driver could do, and consequently, test tolerances are being tightened.
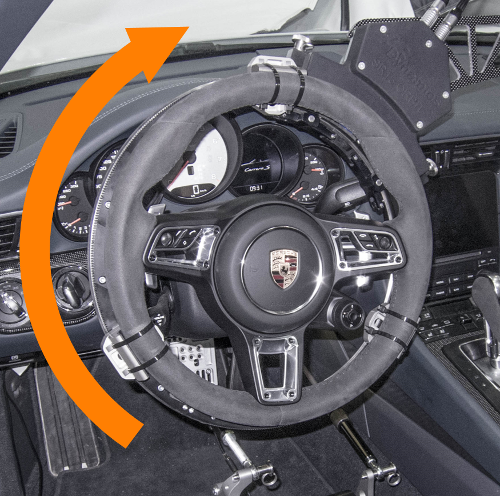
That being said, there is no test in the world which requires steering angle measurement at the accuracy with which AB Dynamics steering robots can measure. Our entry-level model, the SR15, can measure steering angle at a resolution of 0.006˚, that’s 1/60,000th of a revolution. The rest of the range measures steering angle even more precisely (the SR60 can measure 1/600,000th of a revolution!). So why do we use such high-precision encoders? The answer is found in control theory. Our robots are famous for being able to achieve incredible control fidelity; able to turn at high speeds and stop with zero overshoot.
Achieving smooth motion control at a range of speeds is the reason why we need such accurate position feedback. Our motion control operates at a frequency of 4kHz, so we need to know 4,000 times per second where the robot is. The more accurately we know, the more smoothly we can adjust its motion.
And that’s why we measure the steering angle so precisely!