In this guest interview, we speak to Raoul Popescu-Ghimis, Chief Executive Officer of RACE Software, a software package for the development of suspension systems. We discuss the challenges of modern suspension design, the role of simulation in overcoming them and how simulation combines with real-word data to create high-quality digital models. Integrating precise data from a kinematics and compliance (K&C) rig into simulation creates a powerful feedback loop where physical testing informs simulation and vice versa.
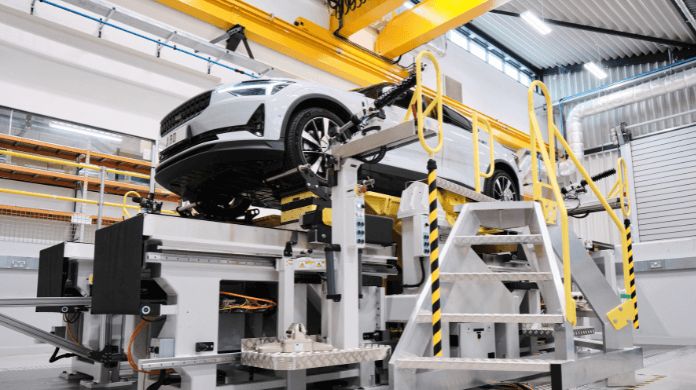
Can you tell us a little bit about your background?
I worked for companies such as Multimatic, HORIBA MIRA, and Jaguar Land Rover, where I developed vehicle chassis and vehicle dynamics for both the automotive and motorsport sectors. With over a decade of experience in the field, and recognising the limitations of traditional vehicle development tools, I teamed up with our CTO, Damien Maher, to bring RACE (Rapid Axle Concept Evolution) Software to life.
What does RACE Software do?
RACE Software specialises in suspension and chassis design, offering multibody dynamics simulation (MBS) solutions. Our platform integrates model building, parameterisation, post-processing, data storage, and report generation into one system. It enables users to complete K&C analysis for an axle quickly. By combining complex physical data with advanced simulation algorithms, our platform allows engineers to predict vehicle performance, significantly accelerating the design process while ensuring precision and cost-effectiveness.
What are the core challenges of suspension design and how does simulation help to overcome it?
Suspension design is inherently complex as it requires balancing multiple, often conflicting factors. Engineers must optimise for ride comfort, handling performance, durability, and safety, while also considering vehicle weight, cost, and environmental impact. One of the key challenges is predicting how the suspension system will perform under a wide range of real-world conditions, including different road surfaces, loads, and driver behaviours. Traditional methods, which involve building physical prototypes and conducting extensive testing, are both time-consuming and expensive.
Simulation helps to address these challenges by enabling engineers to create virtual models of suspension systems, allowing for rapid testing and iteration. By simulating real-world scenarios, engineers can explore different design alternatives and fine-tune suspension performance before any physical prototypes are made. This not only speeds up the development process but also significantly reduces costs associated with physical testing. Furthermore, simulation provides insights that are often difficult, if not impossible, to obtain through physical prototypes, enabling more precise optimisations and improving the final product's overall performance. This approach streamlines the development cycle, enhances innovation, and ensures a higher-quality suspension system.
Could you explain how simulation tools interact with physical data, and why this combination is crucial for optimising suspension design?
By integrating simulation tools with real-world data obtained from physical testing equipment provides valuable insights into how suspension and chassis systems behave under different loads and conditions. It creates highly accurate virtual representations of suspension systems that reflect real-world behaviours.
This integration of physical data and virtual simulation is essential for efficiently optimising suspension design, as it allows engineers to validate their designs early in the development process. Ensuring that the virtual model aligns with real-world performance significantly reduces the risk of costly errors during production. The ability to conduct numerous virtual tests in a fraction of the time required for physical testing allows for greater innovation and engineering excellence in design. By leveraging real-world data, engineers can make informed design decisions, enhance accuracy, and ultimately improve the performance of suspension systems. This combined methodology not only streamlines the design process but also leads to better overall outcomes for both manufacturers and customers.
One of the biggest industry trends at the moment is the move towards electric vehicles. How does this impact suspension design or characteristics designers are targeting?
The current trends towards electric vehicles (EVs) are significantly reshaping suspension design and the characteristics that engineers prioritise. One of the primary impacts of EVs is the increase in weight due to the heavy battery packs and also the shift in weight distribution, resulting in a lower centre of gravity. This necessitates the development of suspension systems that enhance stability and handling while accommodating the unique weight dynamics of electric drivetrains.
Additionally, the quiet and vibration-free operation of EVs places a greater emphasis on ride comfort and noise, vibration, and harshness (NHV) management. Designers are increasingly focused on creating suspension systems and bushings that not only effectively absorb road irregularities, but also ensure a smooth ride experience for passengers.
How important is it to have access to real-world data to support and improve simulation tools?
Working with AB Dynamics is essential for us at RACE Software. Its expertise in providing high-quality, real-world data through the SPMM Plus, is invaluable in refining our simulation models. It allows our simulations to closely mirror real-world performance, creating a powerful feedback loop where physical testing informs simulation and vice versa.
By integrating precise data on vehicle dynamics and suspension performance, we ensure that our simulation tools do not operate in isolation but are grounded in practical performance metrics to enhance the accuracy and reliability of our models.
Our work with AB Dynamics helps to improve the performance of suspension designs, providing greater value to clients and ensuring that our solutions meet the evolving needs of the automotive and motorsport industry.
Can you provide an example where physical data from a K&C machine has been used to improve the correlation of the simulated results?
An automotive manufacturer provided us with a K&C test report and suspension data for a passenger vehicle. Using this data, including suspension geometry and system stiffnesses, we built a virtual model that accurately replicated the suspension system. Where certain stiffnesses were not directly measured, we utilised the K&C report to reverse-engineer these values and adjust the model. By integrating the physical data from the K&C test into the virtual model, we were able to fine-tune critical parameters, resulting in a close match between the simulation and actual suspension performance. This improved the correlation and accuracy, allowing the client to make more confident design decisions.
After the virtual model was correlated, numerous virtual K&C simulations were run to develop the suspension system to meet the new set targets. Once the final design was achieved, a physical prototype was built and validated on a K&C machine before entering production. This process not only improved the workflow but also reduced development time and costs, enabling the client to achieve a suspension system that exceeded their performance targets.
Key takeaways:
- Challenges in suspension design: Modern suspension design involves balancing multiple factors such as ride comfort, handling performance, durability, safety, vehicle weight, cost, and environmental impact.
- Role of simulation: Simulation helps overcome the challenges of suspension design by enabling rapid testing and iteration of virtual models, reducing the need for physical prototypes and extensive testing.
- Using real-world data to improve the quality of simulations: High-quality, real-world data from advanced testing equipment like K&C machines can be used to correlate and improve the accuracy of simulation tools, such as RACE software.
- Integration of physical data: By incorporating real-world data into simulation models, RACE Software ensures accurate virtual representations of suspension systems, improving the reliability and performance of the designs.
- Impact of electric vehicles: The shift towards EVs is reshaping suspension design, with a focus on handling increased weight, lower centre of gravity, and enhancing ride comfort and NVH management.
- Importance of real-world data: Using real-world data to validate designs early in the development process, reduces the risk of costly errors and enhances the accuracy of simulation models.
To learn how AB Dynamics and RACE Software are shaping the future of suspension development, contact us.