AB Dynamics specialises in the design and manufacture of K&C (kinematics and compliance) test machines for the automotive industry. In this blog post Matt Dustan AB Dynamics Director, Laboratory Test Systems, does a deep dive into this technology. He explains exactly why K&C test machines were developed and what they are used for, how virtual testing integrates with them, and what the future of K&C testing holds.
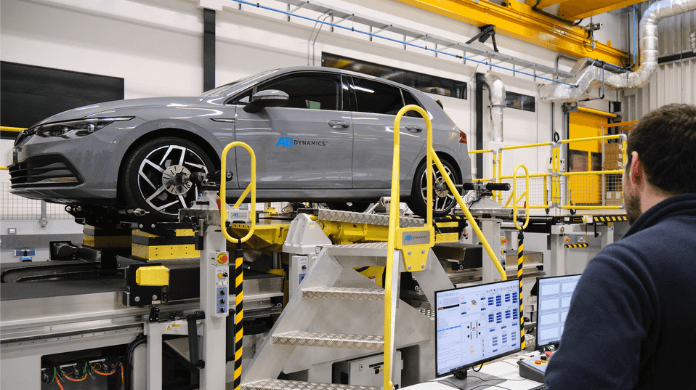
How does K&C testing work?
Before the existence of K&C test machines, there was no standardised method for comprehensively generating the kinematics and compliance characteristics of a vehicle’s suspension system. Instead, to develop physical design adjustments, dynamics engineers had to rely heavily on matching subjective track evaluations with their own experience. K&C machines changed the game by making standardised, objective assessment possible and practical. In essence, a K&C test machine applies very accurate movements and forces into a vehicle’s suspension system. The resulting data provides engineers with a thorough understanding of a vehicle’s ride and handling characteristics.
In most instances, a K&C machine will clamp onto the vehicle’s body and manipulate the vehicle’s wheels to provide the necessary inputs. This enables a combination of roll, pitch, bounce and yaw motion to be applied to the vehicle body to simulate cornering, braking and traction.
However, at AB Dynamics, we do things a little differently. Our K&C test machine, the SPMM, is unique in that instead of moving the vehicle’s wheels to apply the required inputs, it moves the vehicle body, and the wheels remain relatively static. This moving centre table design means the ground plane, which in this case is the road, remains fixed. This more faithfully replicates what happens in the real world because roads don’t move! We can confidently say that this approach results in more accurate data.
What types of K&C tests are there?
There are hundreds of tests that can be conducted on our K&C machine. Some of the industry standard tests include bounce and bounce-pitch, roll, steering, cornering, braking, traction, and lateral and longitudinal compliance. But we also work closely with our customers to create bespoke tests too. For example, horizontal simulation tests that aim to determine the individual contributions of kinematics and compliance effects during lateral and longitudinal manoeuvres, such as cornering and braking.
What are kinematics and compliance test machines used for?
There are lots of use cases for a K&C test machine, it really is a multi-faceted tool. One of the most common use cases is to benchmark competitor vehicles to thoroughly understand the handling characteristics and determine trends in the market. It can be used throughout the vehicle development process to assess suspension systems. It is also used to monitor the performance of early production vehicles to ensure they remain within the prescribed tolerances.
One of our first K&C machines, was installed at Horiba MIRA in 1995 and has tested in excess of 3,000 vehicles, helping to develop next-generation vehicles. Another, being used by a Chinese vehicle manufacturer, is processing more than 150 vehicles every year, including benchmarking and vehicle development activities.
What about virtual K&C testing using simulation?
To do this a multibody simulation (MBS), also referred to as multibody dynamics (MBD), is required. It is a computer-aided engineering (CAE) method used to simulate and analyse the behaviour of mechanical systems. In vehicle dynamics and K&C testing, it replicates a suspension system by modelling interconnected rigid or flexible components linked through joints and actuators. These components interact and move based on applied forces, just as they would during real-world K&C testing, but in a virtual environment.
How does physical K&C testing integrate with MBS?
K&C testing is essential for MBS as it provides real-world data on how a specific vehicle’s suspension performs under various forces. The K&C data allows the MBS model to be correlated to real-world scenarios, ensuring the virtual simulations are highly accurate.
MBS software, such as RACE (Rapid Axle Concept Evolution), offers a cloud-based solution where physical K&C data can be integrated seamlessly. The tests performed virtually in RACE correspond directly to those conducted on AB Dynamics K&C machines, ensuring a precise match between physical and simulated results. This allows engineers to replicate real-world conditions within the virtual environment, fine-tune suspension parameters, and analyse vehicle performance across a range of scenarios.
What is the future of K&C testing and how is it changing?
We are seeing more manufacturers adopting virtual test and validation processes to help accelerate the development of new vehicles. As a result, simulation and digital vehicle models are now critical tools in the development process but correlation with the real world is critical to success. K&C test machines are now being used to generate all the chassis-based data required to create high-fidelity vehicle models.
On top of this, vehicles are also being integrated into Hardware-in-the-Loop (HIL) simulation testing using K&C test machines. This enables a physical vehicle or sub-system of a vehicle to be tested with the resulting data being fed in real-time to an external simulation environment. This is particularly useful for the development of active and semi-active chassis control systems.
K&C testing has been a fundamental stage of automotive development for decades now and with the increasing importance of virtual development and the integration of HiL this is unlikely to change anytime soon.
Key takeaways
- K&C test machines apply very accurate movements and forces into the vehicle’s suspension system
- AB Dynamics’ SPMM K&C test machine is unique as it moves the vehicle body whilst the wheels remain relatively static, therefore faithfully simulating on-road vehicle behaviour
- K&C machines allow an MBS model to be correlated to real-world data, ensuring the virtual simulations are highly accurate
- Manufacturers are increasingly adopting virtual test and validation processes to help accelerate the development of new vehicles
- Vehicles are also being integrated into Hardware-in-the-Loop (HIL) simulation testing using K&C test machines
For more information on our K&C test machines, click here.