AB Dynamics has developed a new active onboard obstacle detection system that makes larger-scale driverless durability and misuse testing possible. It will enable OEMs and testing houses to significantly expand the use of driverless testing to increase testing efficiency, improve data quality and enhance safety.
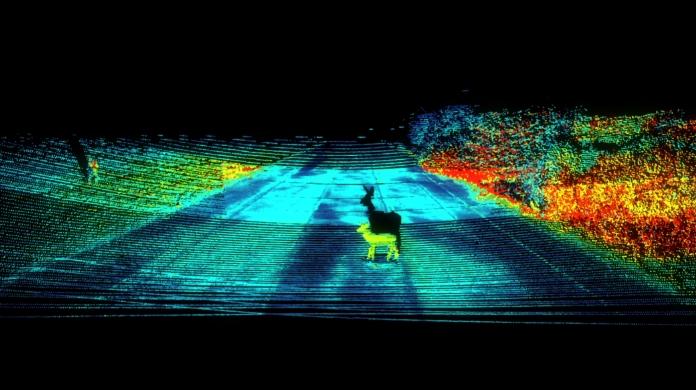
The new active detection system uses sensor fusion from a lidar and dual-camera arrangement to identify objects and their positions ahead of driverless test vehicles. This data is fed to the AB Dynamics controller to stop the vehicle and alert the operator if an object is detected ahead of the vehicle. It allows a larger number of driverless vehicles to be driven safely across a wider area with the same number of operators.
It is the latest enhancement to our driverless durability and misuse testing solution. Driverless testing is most commonly utilised by OEMs to remove the driver from unpleasant durability and misuse testing, such as high-mileage accumulation on Belgian pave or driving over railway sleepers. However, in addition to being a safer testing solution, it also has the benefits of improving efficiency and the quality of data outputs.
“Traditionally, this testing is unpleasant, arduous and sometimes dangerous, which is why driving shifts can be limited to two hours or less to protect the driver,” said Ian Faulkner, Lead Project Engineer. “Our driverless solution completely removes the driver from the vehicle, significantly improving the safety of personnel. It also accelerates testing and the addition of our new active object detection system is the key to increasing this even further by enabling OEMs to adopt this approach on a much larger scale.”
Although proving grounds are usually in remote locations that are closed to pedestrians and other vehicles during testing, test vehicles can often encounter wildlife or debris. The active detection system provides an additional safety layer to protect wildlife and reduce the risk of damage to development vehicles. It also enables the vehicles to be driven ‘out of sight’ of the operator.
The camera and lidar sensors are mechanically mounted using the vehicle’s roof rails, or by an alternative method where roof rails aren’t available. Installation and calibration takes less than 20 minutes, aided by mounts with a built-in adjustable levelling system to correctly and quickly align the sensors. The object detection system can also be easily integrated into existing driverless solutions.
“Safe durability testing has always been a challenge for proving grounds. Even with severe restrictions on testing and driving time, the serious risk to human drivers is never removed,” said Faulkner. “Health and safety is the primary driver for the use of our driverless solutions, but with the maturity of our technology we now see the added benefits of data quality and efficiency helping to justify customer investment.”
Over the last 10 years, we have supplied driverless solutions for use in passenger, commercial, military and mining vehicles worldwide. The system has been designed specifically for flexibility and features multiple layers of integrated safety.
The vehicle’s position, direction and speed are controlled using mechanical actuation of the vehicle’s steering and pedals through driving robots or through Flex-0 drive-by-wire technology. The test route can either be input using GPS data or the vehicle can be driven with the equipment in place to manually record a route to be replayed. Each test can be stored to create a library of predefined scenarios, allowing a full test programme to be quickly selected and executed.
Driverless vehicle fleets are operated from a base station where the operator supervises the vehicles. A high-performance encrypted radio network is utilised to provide reliable data transfer from vehicle-to-vehicle and vehicle-to-base on the proving ground.
“Our driverless solution enables testing to be conducted 24/7 without any dips in performance, only stopping to refuel or recharge the vehicle,” said Faulkner. “Removing the driver from the equation not only increases safety and testing efficiency but the accuracy of our solution enables tests to be conducted that aren’t possible with a human driver. The increased repeatability and consistency also result in better quality data from testing.”
For more information on how we can help support your durability and misuse testing programme, download our latest solution brochure.