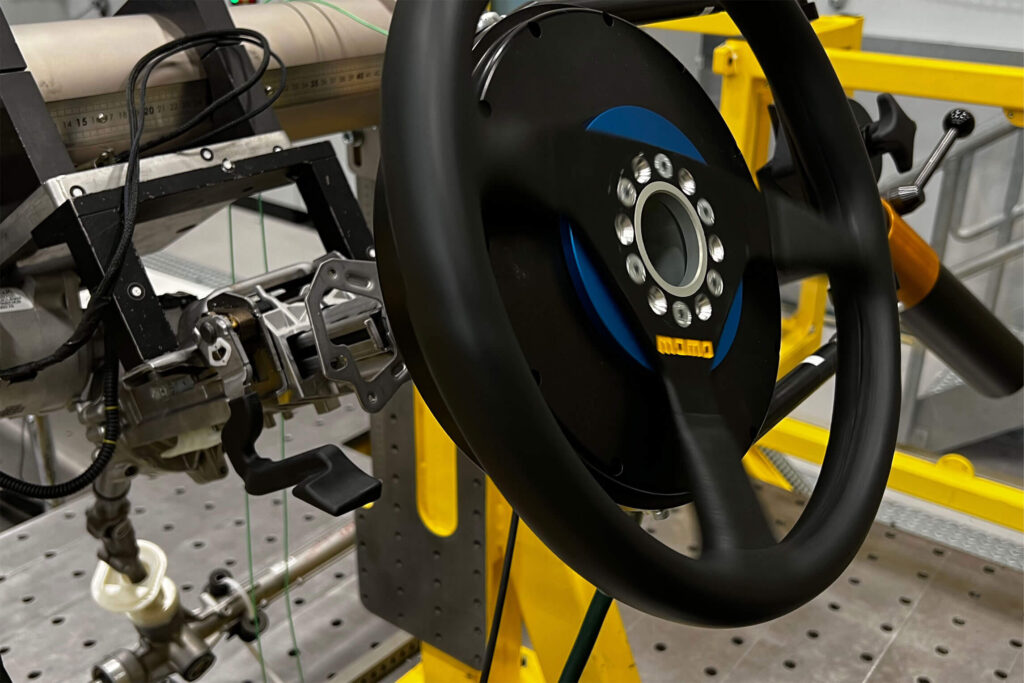
Steering system test equipment
Turning the art of steering development into a science.
Steering system development
The steering system is an important system to a car’s design as it affects the vehicle’s handling, stability, comfort and safety. However, to achieve the desired steering feel, steering system testing typically relies on physical prototypes and track testing, which are costly, time-consuming, and subject to environmental and human factors. Moreover, due to emerging trends in the automotive industry such as electrification, automation, and personalisation, more advanced and flexible steering system testing solutions are required. This is why AB Dynamics has developed laboratory steering system test equipment that can precisely replicate real-world conditions to help accelerate the steering system design process.
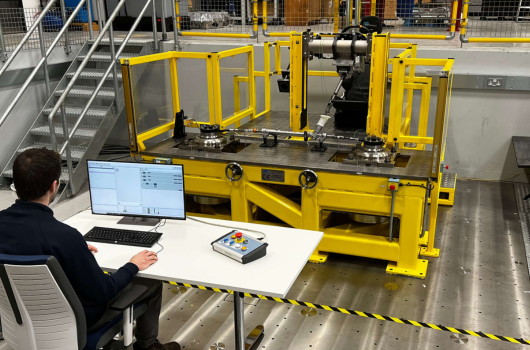
The SSTM
The SSTM is an advanced steering system test machine that enables characterisation, mechanical hardware-in-the-loop (mHiL) and driver-in-the-loop (DiL) activities to be completed on hydraulic, electric power assisted steering (EPAS) and drive-by-wire steering systems. It offers a controlled laboratory environment for assessment, characterisation, and optimisation of steering systems in isolation from the vehicle under development. By subjecting steering systems to simulated independent tie rod forces it precisely replicates real world conditions with minimal latency. With the SSTM, you can accelerate the steering system design process by identifying issues early, reduce costs and deliver an enhanced final product.
How the SSTM works
The SSTM consists of two mounting tables with a high resonance frequency of greater than 150Hz. The front table contains two rotary wheel actuators, one either side of the steering system, and the steering rack mount. The rear table houses the steering column mount, the steering robot and the driver chair. The SSTM uses our industry-leading driving robot to apply inputs into the steering column. To best simulate the geometry of a vehicle, the SSTM uses high-frequency, high-torque rotary wheel actuators to replicate tie rod forces as the inputs into the steering system and highly accurate piezoelectric load cells to measure the resultant forces from the machine.
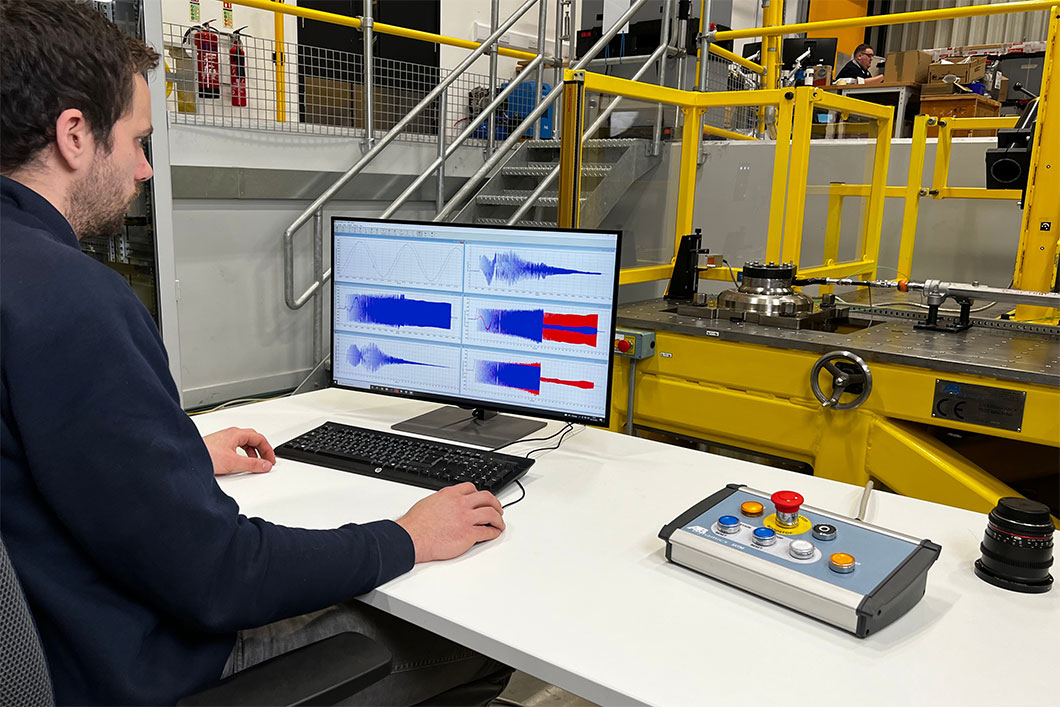
Access immersive testing with a static driving simulator option
With the integration of Ansible Motion’s driving simulator technology combined with rFpro’s simulation environment and visuals, the SSTM becomes a highly advanced driving simulator with the steering hardware fully incorporated. This offers a multitude of benefits especially for ADAS development in Hardware-in-the-Loop (HiL) and Driver-in-the-Loop (DiL) testing. The seamless setup of the steering system and the driver chair to achieve correct vehicle-matched geometry ensures a highly immersive environment for test drivers to subjectively assess the real steering system in simulation. By conducting complex simulated scenarios in the laboratory, you can save significant setup time and costs typically associated with track testing.
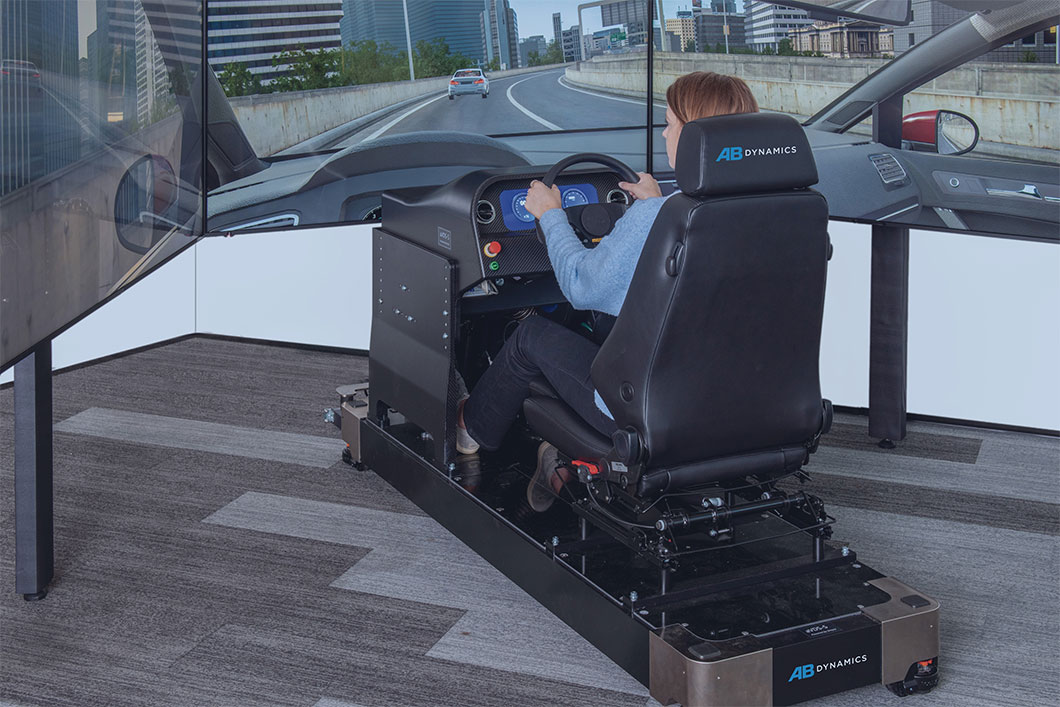
Key features and specifications
- Compensated dual sided tie rod force control for accurate command following
- >40Hz tie rod force control bandwidth
- Electromechanical actuators provide a clean work environment and minimal maintenance
- High natural frequency tables and actuators in excess of testing frequencies
- mHIL capability enables the physical steering system to bypass the steering model during real-time simulations
- Fast changeover between steering robot and OEM wheel for DiL testing
- Drive-by-wire compatible
- Accurate representation of steer system geometry including inner and outer ball joints
Get the SSTM
"*" indicates required fields