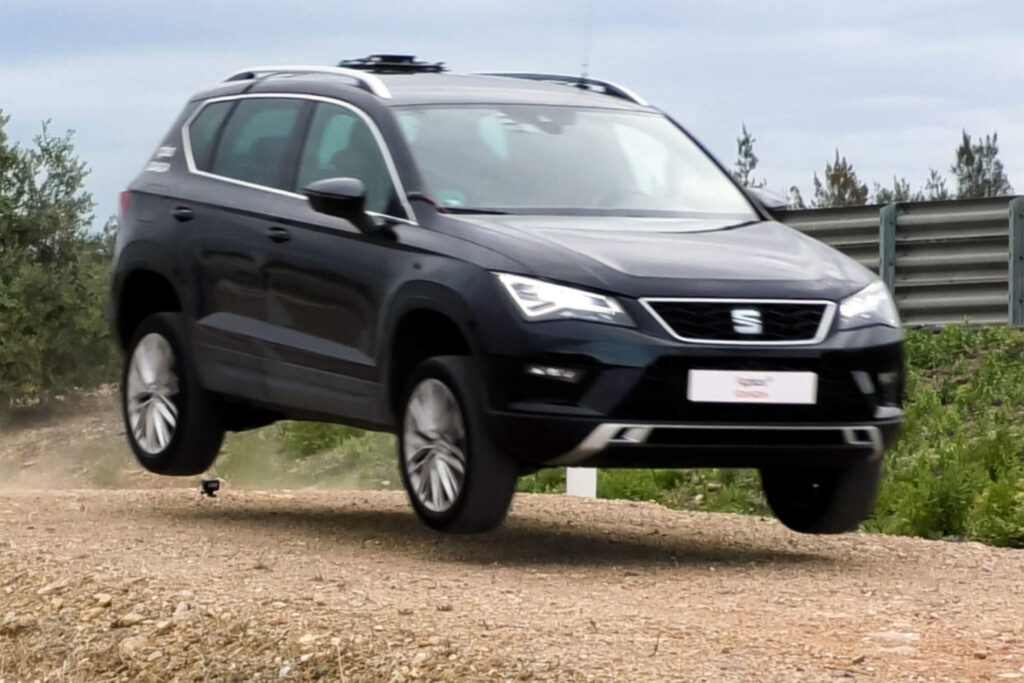
Driverless durability and misuse testing
Remove drivers from risk, increase efficiency and improve test data quality.
What is driverless durability and misuse testing?
Durability and misuse testing are integral to understanding vehicle performance. Durability tests, designed to accelerate the wear of vehicle components, typically involve repeatedly driving a vehicle over rough surfaces. Misuse tests, on the other hand, are designed to explore what happens to a vehicle in extreme situations, such as when driving into a sandbank or over a ramp and becoming airborne.
Durability and misuse test programmes are physically arduous and potentially dangerous, often requiring large teams of drivers due to the limited testing times each driver can endure. This is why we offer a driverless solution, which not only eliminates the risk of fatigue or injury to test drivers but also provides repeatability, accurate speed and path following.
Our driverless durability and misuse solution
AB Dynamics’ driverless solution uses driving robots, software, telemetry and sophisticated controllers to safely conduct these tests, removing the driver from the vehicle. It eliminates risk to the driver, accelerates testing and improves the accuracy and repeatability of test results.
Our driverless solution is comprised of three key elements: the driverless vehicle, the base station and the communication network. In addition, a LiDAR-based active collision detection system can be optioned to detect and avoid untracked objects on the test track.
Download brochure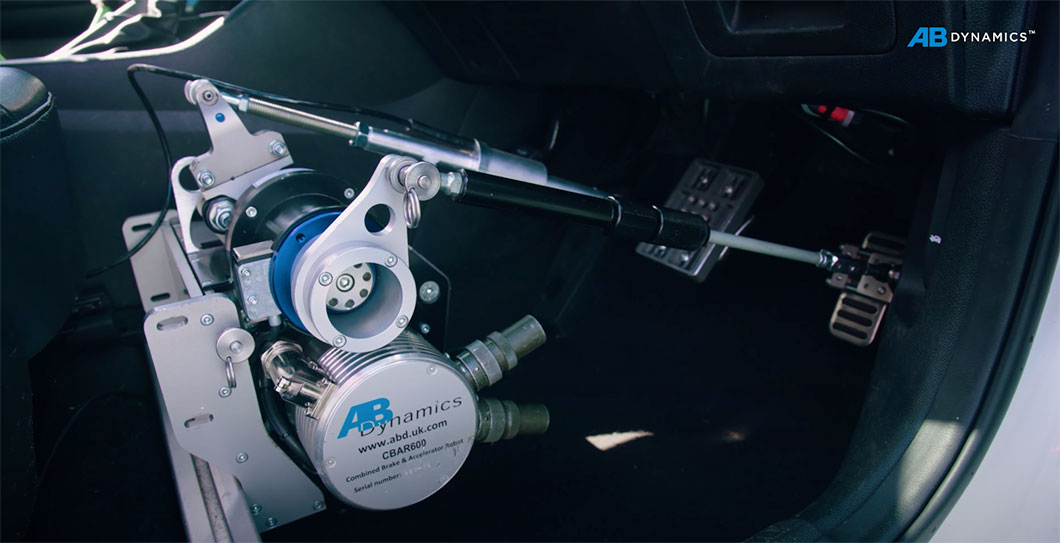
You are currently viewing a placeholder content from YouTube. To access the actual content, click the button below. Please note that doing so will share data with third-party providers.
More InformationDriverless vehicle
Driving over rough surfaces for extended periods can have a cumulative effect on a human driver’s health. In our solution, vehicles are made driverless through either mechanical actuation using pedal, steering and gearshift robots, or by-wire using our Flex-0 CAN control system. Both robot actuation and by-wire solutions provide precise control of the vehicle’s position, direction and speed, ensuring repeatability and accurate data.
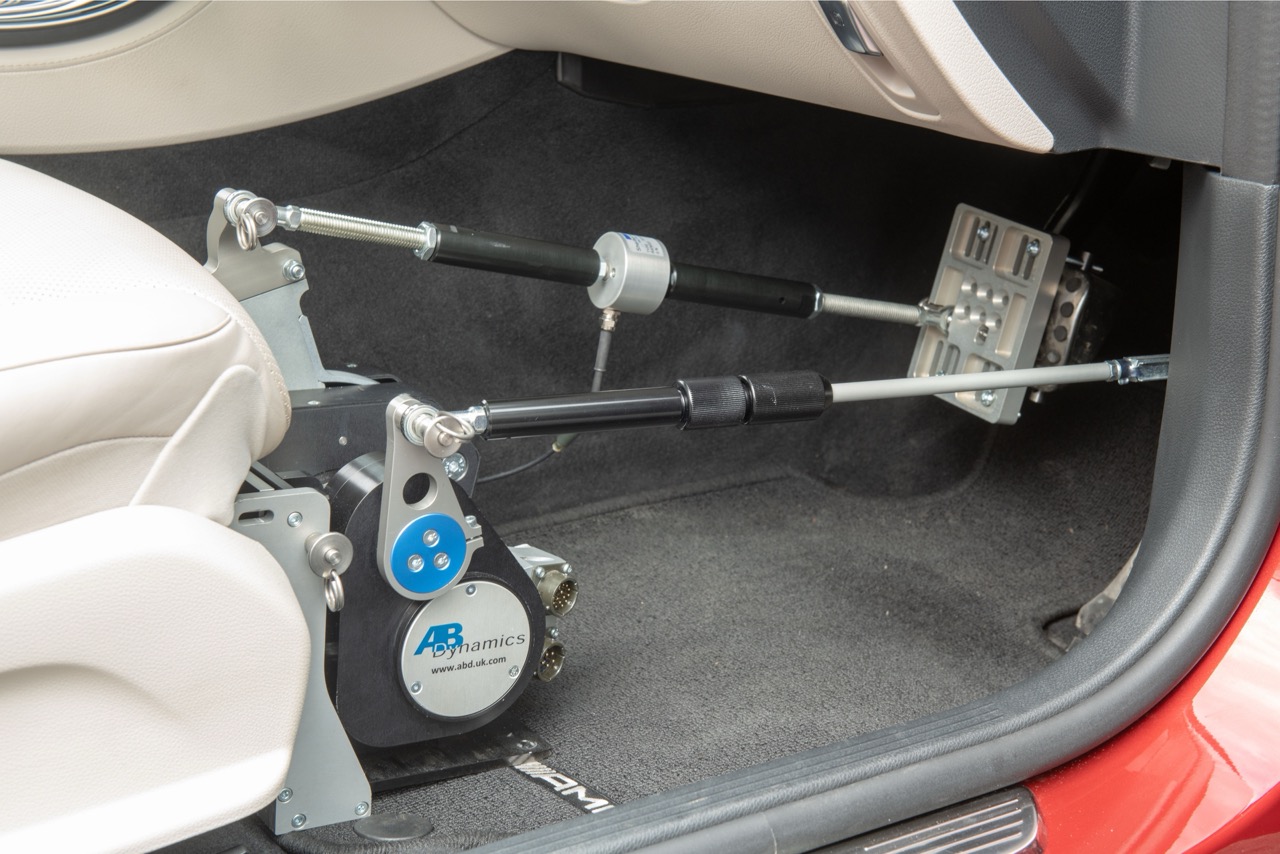
Base station
The base station is where the operator manages and controls vehicles using AB Dynamics’ easy to use Ground Traffic Control (GTC) software. Durability test drivers can learn the location of the most uncomfortable features on the track and deliberately avoid them. However, our driverless solution avoids this problem because vehicle test routes are created and executed using our Path Following software. It uses real-time feedback from GNSS-corrected motion packs to provide the inputs to the driving robots or Flex-0 to precisely guide the vehicle along the specified path.
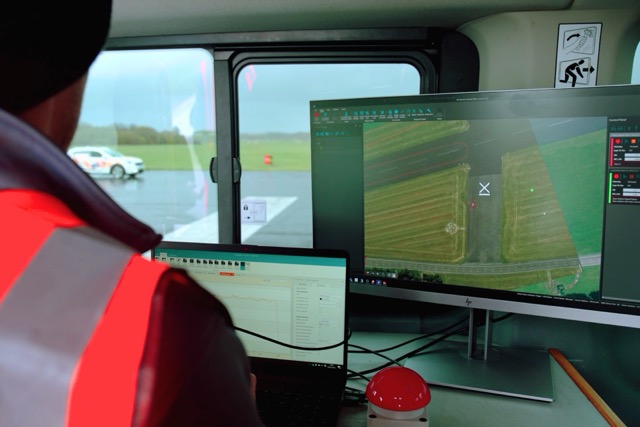
Communications network
The system utilises a high-performance mesh radio network to provide reliable data transfer from vehicle-to-vehicle and vehicle-to-base. Cyber security is ensured through encryption, while the network can be set up with fixed infrastructure or it can use mobile nodes to enable testing anywhere.
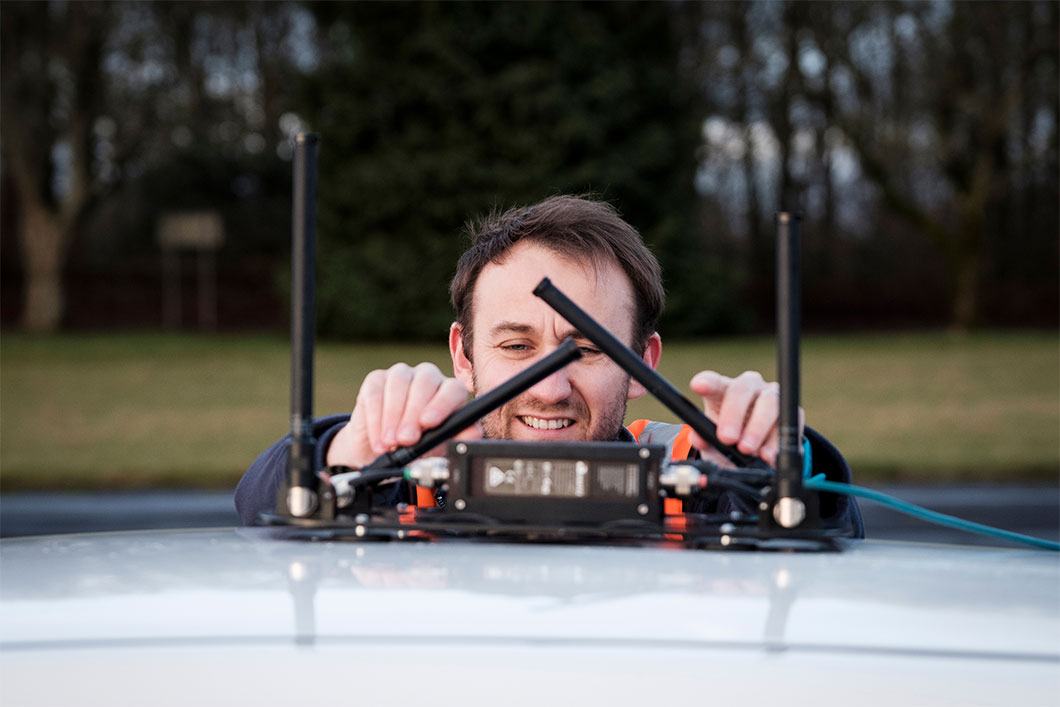
Latest case study
Need to discuss your durability and misuse testing requirements?
"*" indicates required fields